Challenges in achieving successful mega projects
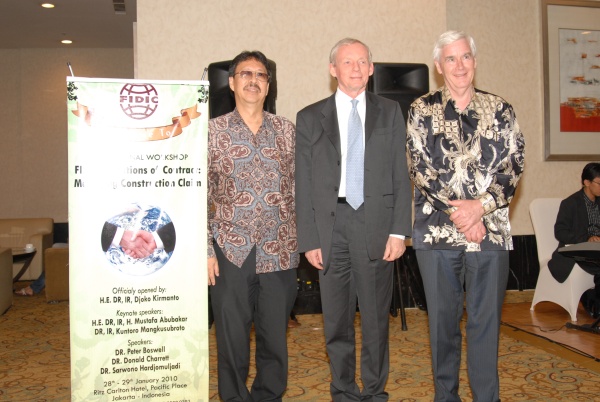
by Dr Donald Charrett and Philip Loots
Loots & Charrett Pty Ltd
Megaproject are projects with a capital cost in excess of US$1bn. On one estimate, 65 per cent of megaprojects are failures. Project scoping and risk allocation are central to improving outcomes.
Introduction
Megaprojects are increasingly common around the world. For the purposes of this article, a megaproject is a project with a capital cost in excess of US$1bn. Megaprojects are large-scaleprojects involving substantial capital expenditure and cash flow, and a correspondingly large design, procurement and construction workforce that must be appropriately managed. Further, the scale and number of interfaces in a megaproject necessarily imply a level of complexity greater than in smaller projects.
The financial significance of megaprojects to their owners is self-evident: they consume large amounts of capital that is invested for anticipated future income streams (in the case of private enterprises) or for the provision of efficient public infrastructure (in the case of government enterprises). Whether publicly or privately funded, project sponsors are looking for efficient deployment of capital to produce successful projects.
Notwithstanding the importance of megaprojects to their sponsoring organisations – and to the contractors who build them – there arewell-documented examples of unsuccessful megaprojects that have destroyed billions of dollars of capital.1 The scale of such capital destruction in some cases has resulted in the insolvency of the sponsoring company or the contractor.
Detailed studies of construction projects around the world have revealed a disturbing fact: the success rate of megaprojects is less than the success rate of smaller projects. These studies have identified a number of factors that have contributed to the lack of megaproject success. This article discusses the findings of recent research in the hope that lessons can be learned from past unsuccessful projects to ensure that future megaprojects have a higher likelihood of success.
Project success and failure
The authors have previously discussed examples of unsuccessful projects, where that term was applied to projects that did not fulfil their expectations, or more specifically, where there was an unacceptable difference between expected and observed performance.2 This definition includes unacceptable shortcomings in the execution time, cost or quality of a project. In this context, quality encompasses not only the quality of construction in respect of materials and workmanship, but also the design and whether the completed project fulfils the expectations for functionality and performance.
Merrow assessed the success or failure of 318 industrial megaprojects (projects that make a product for sale with a total capital cost of more than US$1bn), based on a detailed analysis of their performance. In his assessment of these megaprojects, Merrow used measurable criteria to assess project success or failure. He characterises an industrial project as a failure if it exceeds one or more of the following cost, time and quality thresholds:
- actual final cost exceeds the cost estimate made at the project sanction stage by more than 25 per cent;
- project spends more than 25 per cent greater than other projects with similar scopes;
- the execution schedule slips more than 25 per cent from the schedule forecast at project sanction;
- the project execution schedule is greater than 50 per cent more than the length of execution relative to similar projects; or
- there is significantly reduced production relative to that planned into the second year after mechanical completion.3
The reported outcome of this assessment is quite surprising. Only 35 per cent of the megaprojects were successful, and these tended to be genuinely excellent projects on the time, cost and quality criteria. However, the 65 per cent of megaprojects that were considered to be failures:
- averaged 40 per cent cost overrun whilst being very expensive in absolute terms;
- slipped their execution schedule by an averageof28percentwhilstbeing15percent slower than a competitive schedule; and
- averaged only 65 per cent of planned production in the first year.
The 140 projects in the oil and gas production sector (41 per cent of the projects assessed) fared the worst of all. Of these megaprojects, 78 per cent were assessed as failures: cost overruns averaged 33 per cent; cost competitiveness was almost 40 per cent more than the industry average; and nearly two-thirds suffered severe operability problems. Minerals megaprojects failed around 70 per cent of the time, and had poor operability and cost growth.4
A survey of Australian construction projects in 2006 provided data on time and cost outcome of projects, based on quantitative research. Only 56 per cent of all projects surveyed were completed on time: 66 per cent of projects in theAUS$20m–AUS$50m range were completed on time, whereas only the scale and number of interfaces in a megaproject necessarily imply a level of complexity greater than in smaller projects 50 per cent of projects valued at over AUS$500m were completed on time.5 The 2006 survey revealed that 38 per cent of projects were completed over budget. D&C contracts performed better than construct-only projects in this regard: 33 per cent of D&C projects exceeded their budget, by an average of 15 per cent, whereas 46 per cent of construct-onlyprojects exceeded their budget, by an average of 19 per cent.6
Australian research
A major Australian law firm collaborated with the Australian Constructors Association in 2006, 2008, 2011 and 2014 (and with Infrastructure Partnerships Australia in 2006, 2008 and 2011) to carry out surveys of the Australian construction industry that were reported in four ‘Scope for Improvement Reports’ (the ‘Reports’).7 These surveys involved more than 120 respondents, representing the spectrum of participants in Australian construction and infrastructure projects: public and private sector principals, contractors, consultants, financiers and industry bodies.
The Reports are valuable not only for their identification of issues that have contributed to unsuccessful projects, but for their constructive suggestions as to how these issues can be addressed to achieve more successful projects in the future. The timeframe spanned by these Reports covered the build up to and execution of an unprecedented number and scale of megaprojects in the Australian resources industry. For example, there were seven LNG plants with a total capital value of over AUS$200bn under construction in early 2015.
The 2006 Report identified five ‘pressure points’ – issues that inhibit project delivery and create stress on a project or its participants. The 2014 Report also identified five pressure points, three of which were in the 2006 Report:
- a shortage of skilled resources;
- inadequate scoping; and
- poor risk allocation.
Two new pressure points were identified in 2014: productivity; and costs of tendering. These issues, and the shortage of skilled resources, are specific to Australian conditions and may be related to the unprecedented demands on the construction industry arising from the boom conditions. Productivity and the shortage of appropriately skilled resources may impact the competitiveness of Australian megaprojects with those in alternative locations. However, they are external to any particular project; as longer term issues they need to be addressed on anindustry-wide basis.
International research
Merrow identified seven key mistakes that companies make in developing and executing megaprojects:
- project sponsors endeavouring to retain all of the benefits of a project without adequate regard to the legitimate interests of other stakeholders;
- an aggressive project schedule that does not pay sufficient attention to project requirements;
- project development carried out without alignment with the underlying business deal;
- insufficient time and money invested in investigating the project’s viability and feasibility prior to the final investment decision to sanction the project (front end loading);
- reducing cost estimates to satisfy investment criteria;
- transfer of cost and schedule risk to contractors; and
- terminating project managers of projects that overrun their budgets.8
What can be done to improve megaproject outcomes?
The various studies referred to have identified a number of issues that need to be addressed to improve project outcomes. This paper focuses on just two, scoping and risk allocation, issues that are within the control of the principal. These issues were addressed in detail in the 2008 and 2011 Reports respectively.
The evidence shows that, when properly executed, megaprojects can be an outstanding success
Project scoping
Scoping is the process of determining the contractual expression of an owner’s project requirements. It involves the identification of the fundamental objectives of the project; development of the project requirements in the form of functional and performance outcomes and/or specific technical requirements to achieve those objectives; selection of the most appropriate contractual model and risk profile; and translation of these requirements into appropriate contractual scope documents for the project.9
Merrow uses the term ‘front end loading’ for the period in which the scope and execution detail of a project are defined before a final investment decision is made. He notes that adequate front end loading is expensive (three to five per cent of project cost), but is essential to successful projects as it drives cost and schedule predictability and minimises operational problems. The authors concur with Merrow, who considers that scope development, the second of the three phases of front end loading, is the most important stage in any project’s development.10
Preparation of the project scope is based, implicitly and explicitly, on the required ‘quality’, which includes performance, functionality, durability, maintainability and operability. Selection of the appropriate quality will often involve a trade-off in determining the appropriate balance between schedule, cost and quality. A clear, well-defined project scope is necessary to produce a realistic cost estimate. It follows that cost estimates produced prior to project scoping will be unreliable. Further, if the scope subsequently changes, the costs will inevitably change.
The same applies in relation to the project schedule – a reliable schedule can only be prepared when the project scope has been defined. Subsequent significant changes in scope indicate that the project schedule will need to be reassessed in the light of those changes, which may impact the time in which the scope can practicably be executed.
Thus, in one sense, quality is an input into the scoping exercise, and cost and schedule are outputs from the process. However, as iswell-known, there can be a complex trade-offbetween time, cost and quality in a project. Merrow presents a graph showing how changes in a project’s internal rate of return are related to changes in operability (‘quality’), capital cost and schedule. This graph shows, for a target of 15 per cent real return on investment and constant market factors, that operability and capital costs have a far greater impact on internal rate of return than schedule. For example, a 30 per cent growth in capital cost results in investment returns of less than ten per cent, below a typical company’s cost of capital. However, it would take more than a five per cent schedule improvement for every one per cent of additional cost for the return to be investment neutral.11 However, sometimes the additional cost of acceleration is necessary to address the bigger risk of failure to honour product sales contracts because of delayed completion.
Merrow emphasises that the targets for cost, schedule and quality must be established at the point when they are at least feasible in principle and will result in a valuable outcome for the project. He identifies three misguided trade-offsthat frequently result in project failure:
- quality is sacrificed for low cost;
- cost is sacrificed for fast schedules; and
- quality is sacrificed for fast schedules.12 The 2006 Report highlighted that poor scoping at the outset of a project almost inevitably resulted in cost overruns, delayed completion and disputes. The 2008 Report identified a number of factors that result in poor scoping of Australian construction and infrastructure projects:
- lack of experienced and sufficiently competent personnel;
- insufficient time to prepare the scope documents;
- inadequate definition of project objectives by the principal, resulting in subsequent changes to the scope;
- corrections to scope documents;
- lack of consultation with end-users; and
- insufficient site information.13
The 2008 Report identified 16 practical steps for successful scoping, consistent with many of the front end loading issues identified by Merrow, including:
- clearly identify project objectives;
- bring together all relevant stakeholders and end users for the project;
- set realistic timeframes and budgets;
- interface the proposed project with related projects and existing infrastructure;
- manage the interplay between project scoping and the statutory environmental and planning approval process;
- clearly describe the project objective and requirements once identified;
Three misguided trade-offs that frequently result in project failure [are]: quality if sacrificed for low cost; cost is sacrificed for fast schedules; and quality is sacrificed for fast schedules
- choose the right approach for scope description; and
- choose the right contract delivery model.14 The consequences of inadequate scoping of a project before a construction contract is entered into arewell-known. Changes to scope during construction are inevitably disruptive,time-consuming and costly to implement via variations. Further, they frequently lead to disputes that are a distraction to the parties’ project delivery aspirations, are time-consumingand expensive to resolve, and adversely impact their working relationship.
These consequences were revealed in the 2008 Report: 61 per cent of respondents said that inadequate scope documents resulted in a cost overrun, with more than half of those overruns costing more than ten per cent of the value of the project and a third more than 20 per cent. For megaprojects with a value of over AUS$1bn, approximately one quarter experienced a cost overrun of more than 20 per cent of project value because of inadequacies in scope documents.
Risk
The definition of risk in Australian Standard AS4360:2004 is ‘the chance of something happening that will have an impact on objectives’. Whilst that definition includes positive as well as negative impacts, consideration of risk in construction contracts usually refers to adverse impacts. A variety of risks are inherent in any construction project, and they need to be identified, allocated and managed.
It is a widely accepted principle that in a construction contract, each risk should be allocated to that party in the best position to manage and control it (the Abrahamson principle). It is also generally accepted that for each risk assumed by the contractor in a construction contract, a rational contractor will include the ‘price’ of that risk in its tender price. The price that a contractor puts on a particular risk will, however, vary with market circumstances. In the authors’ view, under certain market conditions, not all contractors can be expected to be ‘rational’, so bid evaluation procedures should make appropriate allowances for this.
Risks need to be identified before they can be allocated or managed, and the time to do that is during the scoping process. One of the potential consequences of applying inadequate time and resources to the preparation of a project scope is that significant risks may not be identified. The 2011 Report stated that in nearly 30 per cent of projects, key risks were first identified only after contract signing.
The allocation of risks between principal and contractor is an area of significant contention. As the party generally preparing the tender and contract documents, the principal is normally the one that determines the allocation of risks in the construction contract. For a variety of reasons, principals are increasingly reluctant to assume many risks that, traditionally, have been their responsibility. Many contractors feel that they are inappropriately forced to assume many risks that they are unable to control or manage. Further, the competitive tendering environment means that they are unable to appropriately price these risks.
Respondents in the 2011 Report identified the following key risks as commonly allocated in an inappropriate manner:
- time for completion/delay;
- design;
- scope inadequacies; and
- site conditions.
Various consequences may arise from the inappropriate allocation of risks, and these will vary depending on the economic and individual circumstances. In a sellers’ market, a contractor will put a high price on risks to ensure that its profit margin is preserved in the event that the risks eventuate. To the extent that risks do not eventuate, the principal has paid a high ‘insurance’ price that results in a windfall profit to the contractor, an outcome that may be acceptable to the principal. Conversely, in a buyers’ market where the contractor has not adequately priced the risks (because of competition for contracts or because the risks have not been identified), the principal makes a windfall gain by not paying for the real cost of the risks. However, that windfall gain comes with a new set of risks for both principal and contractor, arising from the contractor being unable or unwilling to perform its contractual obligations.
Where unpriced (or inadequately priced) risks eventuate, the contractor may suffer substantial delay and/or monetary loss that put quality, schedule and completion at risk. Such circumstances will inevitably result in additional claims that have to be managed and may also trigger a formal dispute. In a worst-casescenario, where the contractor has insufficient balance sheet strength to absorb the loss, the principal may be forced to terminate the contract.
Management of risks during the execution of a project is an ongoing exercise. There are a variety of appropriate project and contract management tools that need to be applied. Many provisions in modern construction contracts are written to ensure that risks are appropriately managed when they do eventuate. Early warnings, strict time limits on notification of events or circumstances, risk registers, timely processing of claims and formal monthly reports are just some of the tools currently used. The formal procedures for contract administration in many modern construction contracts define a process for good risk and project management. Complying with them is not only required as a matter of law, it will also minimise the adverse consequences arising from the eventuation of risks.
Conclusion
Various studies have shown that , notwithstanding their high cost and importance, megaprojects have a poor track record of performance, not only in absolute terms, but also with respect to projects of lesser value. The evidence shows that, when properly executed, megaprojects can be an outstanding success. However, the substantial number of megaprojects that have failed on time, cost and quality criteria suggest that we should be learning their lessons so that future megaprojects will be more successful.
This article has touched on two important issues that are important for the success of any project, but are critical to the success of megaprojects.
The proper definition of the scope is the essential foundation of a megaproject. Without it, the principal will not have defined its fundamental project objectives, nor will it have incorporated its requirements in appropriate contractual form.
Inadequately prepared scope is likely to lead to expensive and time-consuming variations, delay, claims and possible disputes. Proper scoping requires adequate and appropriately skilled resources, and sufficient time to identify comprehensively all of the relevant issues.
Project risks are those issues that have the potential to impact adversely the anticipated project outcomes. They need to be identified at the earliest stage during scoping, appropriately allocated to one of the contracting parties (preferably the one best placed to manage and control them), and then managed appropriately with adequate resources during project execution. Adherence to the formal contract requirements for notification of issues, regular reporting and claims is generally fundamental to successfully managing those risks that, inevitably, eventuate during the execution of any megaproject.
Notes
1For example, Merrow refers to the failure of BHP’s Hot Briquetted Iron Project in 1999 that contributed to the company losing more than half of its market value, as well as unsuccessful projects conducted by Shell and BP that resulted in substantial capital losses: Edward W Merrow,Industrial Megaprojects (2011), 12.
2Philip Loots and Donald Charrett, Practical Guide to Engineering and Construction Contracts (2005), 333–358.
3See n1 above, 37–38.
4See n1 above, 48–49.
5Blake Dawson Waldron Lawyers, Scope for Improvement: A Survey of Pressure Points in Australian Construction and Infrastructure Projects (2006), 24.
6Ibid, 24–26.
7Blake Dawson Waldron Lawyers, Scope for Improvement: A Survey of Pressure Points in Australian Construction and Infrastructure Projects (2006); Blake Dawson, Scope for Improvement 2008: A Report on Scoping Practices in Australian and Infrastructure Projects (2008); Blake Dawson, Scope for Improvement 2011: Project Risk – Getting the Right Balance and Outcomes (2011); Ashurst Australia, Scope for Improvement 2014: Project Pressure Points – Where Industry Stands (2014).
8See n 1 above, 2–8.
9Ashurst Australia, Scope for Improvement 2014: Project Pressure Points – Where Industry Stands (2014), 31.
10See n 1 above, 101.
11Ibid, 108.
12Ibid, 110.
13Blake Dawson, Scope for Improvement 2008: A Report on Scoping Practices in Australian and Infrastructure Projects
(2008), 7–8.
14Ibid, 8–9.
——————————-
Dr Donald Charrett is a barrister, arbitrator and mediator practising in building and engineering disputes, arbitration/ mediation/expert determination, construction law, commercial law, contract law, insurance law and professional negligence. He is based in Melbourne, Australia, and can be contacted atd.charrett@me.com
Philip Loots is counsel for Bechtel WA Pty Ltd, a graduate of Harvard Business School’s Program for Management Development, and an Associate Adjunct Professor at the Centre for Mining, Energy and Natural Resources Law, Faculty of Law, University of Western Australia. He can be contacted at ploots@bechtel.com